|
|
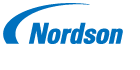 |
Nordson Extrusion Dies Industries designs, manufactures, and reworks precision tooling used in plastics processing and web converting. |
Employees : |
100-500 |
Year established : |
1971 |
Business : |
Manufacturer |
Nordson Extrusion Dies Industries designs, manufactures, and reworks precision tooling used in plastics processing and web converting. The company is a global supplier of flat die systems for extrusion, coextrusion, and fluid coating. EDI also builds or reworks tooling for other processes, such as blown film extrusion, coextrusion blow molding, and strand palletizing. From its world headquarters in Chippewa Falls, Wisconsin, U.S.A., EDI exports more than half of the dies that it manufactures. Its subsidiaries, EDI GmbH in Germany and EDI China, provide sales and technical service, parts, and die rework. Visit EDI online at www.extrusiondies.com.
| Adjustable Geometry Coextrusion Feedblocks This entirely new and highly effective method for layer combination and profiling has revolutionized the industry. Layers pass through precisely sculptured inserts that are housed in the Combining Spools. Fine adjusters allow these Combining Spools to be rotated to vary both the height and width of the tapered exit geometry for each layer, providing robust on-line control of layer uniformity in the final product. In addition, optional thermal profiling capability is possible through a series of miniature heaters that may be installed downstream of the combining point. |
| Ultracoat II Precision Slot Die Coating Heads For applying low-viscosity or wet coating materials, Ultracoat dies provide greater precision than roll-coating systems. Since all of the coating material is applied to the substrate in a metered fashion, significant savings in raw materials can be realized. EDI's dedicated clean room for optimum grinding ensures die flatness, so that coat weight uniformity can be maximized. Ultracoat II dies incorporate a flexible lip feature to refine coat weight distribution across the substrate and are available with manual or automatic lip adjusting mechanisms. A variable offset between the wet-side and dry-side lip faces can be achieved utilizing supplied shims. Application-specific lip face designs are available. | |
|
|