|



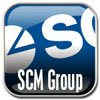
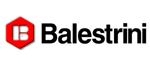 |
 |
# Zariadenia na odporové zváranie
# Stroje na bodové zváranie
# Pištole na bodové zváranie
# Zariadenia na odporové zváranie |
rok založenia : |
1985 |
typ obchodu : |
Manufacturer |
Matuschek Messtechnik GmbH bola založená v roku 1985 Dr U. Matuschek. Spočiatku firma zaoberá vývojom elektronických meracích komponentov pre priemyselné aplikácie.
Medzitým spoločnosť špecializujúca sa na oblasť technológií odporového zvárania. Prvýkrát účinné metódy na kontrolu zváracieho procesu boli vyvinuté. Intenzívny rozvoj tejto technológie sa Matuschek Messtechnik jedným z príslušných výrobcov strojov v tejto oblasti.
Spoločnosť pôsobí po celom svete od Alsdorf, Nemecko. Zvýšené používanie našich strojov a globálnej expanzie boli dôvodom na založenie Matuschek Zváranie Products Inc v USA v roku 2005.
| collector welding "hot staking" This method is used for contact points which are accessible only from one side, where the contact electrode approaches - single-sided and from the top - close to the welding electrode.
The loose leads are positioned over each other in a slot which has been slit into the collector. This method is applied in serial production of small-power motors using mechanised or automated welding machines and belongs to the field of resistance welding of enamelled wires.
|
| resistance welding of contacts In resistance welding of contacts, in general, dissimilar materials are to be joined. To this end, copper and brass alloys are used as insulators, however, depending on the application, also steel sheets with different metal coatings are used. The contacts normally consist of a material with a good conductivity (copper, silver, gold, etc.) which is, on the one hand, advantageous for the functioning of the produced parts but which, however, puts demands on the welding technique.
Moreover, the contacts are normally produced with so-called high-speed machines with very high clock rates. The welding power sources which are used for this process must fulfil the following demands:
high welding currents, dependent on contact geometry and material
high duty cycle
controlled, very short welding times
integratable into different machine concepts
online monitoring
The high-frequency inverters of the SPATZH6000 series are particularly suitable for this application as they meet all the above-mentioned demands. The individually settable limit value- and alarm management of these power sources guarantee the steady, good quality standards of the produced parts
|
| Resistance Welding of Lamps Very thin foils made of exotic materials are welded with ultrafine wires and wire spirals which are hardly visible. Every single welded joint must be of good quality, since every single welding point is decisive for the function and lifetime of the lamp.
Here, also extremely "smooth" welding currents are required in order to prevent preliminary damage of these susceptible materials through current surges. For cross wire welds inside the lamps, tight tolerances during wire penetration are requested.
The above-mentioned demands are reliably fulfilled with the high-frequency inverter of the SPATZ series. The standard equipment comprises also the measurement inputs for current, voltage, force and displacement signals which allow reliable inline control of the process data
| |
masdat
Click on our Logo to view this Catalog
|
|
|